Talk about inflation and supply chain is all the rage these days. How do these two factors interact? How exactly does supply chain disruption cause inflation?
Fortunately, there’s a game for that: The Beer Game.
For a game with the word “beer” in its name, The Beer Game is not very fun. I would say it comes in a pretty distant second to beer pong.
For a game about supply chains, The Beer Game is actually quite fun so everything’s relative I suppose.
The set up of the Beer Game is pretty simple: there are four players (some can be computers) in a four-step supply chain: the manufacturer/brewer, the distributor, the wholesaler, and the retailer.
The brewer makes the beer, the distributor buys it and bottles it then sells it to the wholesaler. The wholesaler sells to the retailer whole ultimately sells it to the end consumer.
Consumer demand flows the other way: The retailer gets orders and passes them onto the wholesaler that passes them along to the distributor and finally the brewer/manufacturer.
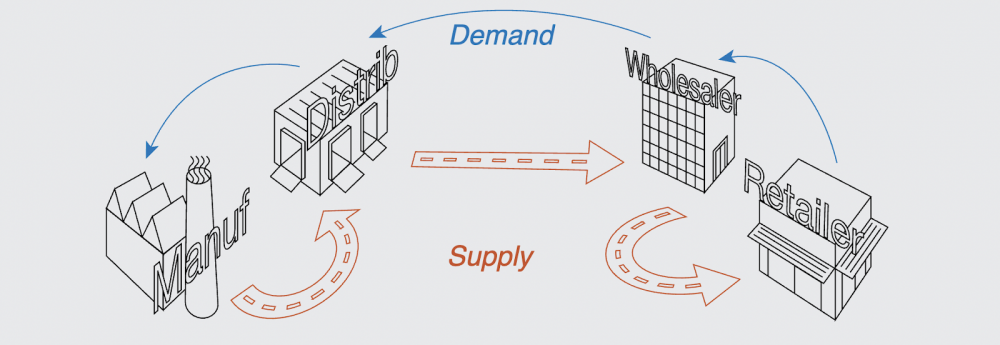
The goal for each player is to have the “right” amount of inventory. You want to have enough to be able to fulfill incoming orders, but not too much as you also want to minimize inventory costs.
Inventory-based businesses don’t want to have too much on stock because inventory costs money to store and ties up cash flow (and, in some cases, can spoil). You also don’t want to have too little in stock because you are losing sales.
The theoretical ideal then is the “just-in-time” supply chain where each piece of the supply chain has exactly the right amount of inventory at the right time.
This seems like a simple problem, but there is one wrinkle in the Beer Game: there is a two-week communication gap toward the upstream and a two-week supply chain delay of product towards the downstream.
For example, let’s say you are playing as the wholesaler. The wholesaler wants to buy exactly enough inventory from the distributor so that they can deliver the exact amount needed to the retailer.
The wholesaler can’t communicate with the retailer except to see the incoming orders. So, on any given turn (representing a week), the wholesaler will see how many orders that the retailer placed in the previous week. They will need to deliver that quantity the following week.
It’s not so easy to just place an order for that amount with the distributor because of the delay.
Let’s say I am playing as the wholesaler and see that the retailer wants 10 cases of beer shipped to them next week.
If that same week, I place an order then for ten cases of beer with the distributor then it won’t arrive at the distributor until next week, then it won’t arrive back to me until the following week then I can’t deliver it to the retailer until the week after that.
If the end demand is fairly steady, then it’s pretty easy to know how much to order. Let’s say the retailer is ordering between 8-12 cases of beer every week from the wholesaler. As the wholesaler, it’s pretty easy to forecast your demand.
You want to make sure you have about 12 cases in stock at any time so that you can fill the order without holding too much excess inventory. (Even this is trickier than it sounds, but still somewhat solvable).
Where things start to break down is when you get big swings in end-user demand. Let’s say in week 1 the retail orders ten cases. As the wholesaler, you assume that is about how much beer the retailer normally orders so you then order ten cases from the distributor.
The next week though, the retailer orders forty cases. The wholesaler only has ten cases in stock and ten more coming so they can’t fulfill the order and have a backlog of twenty cases they need to deliver. They’re losing out on sales!
Worrying that demand has now increased dramatically, the wholesaler then orders sixty cases from the distributor – twenty cases will be used to fill the backlog and the wholesaler is expecting another order for forty cases and wants to make sure they are in stock.
Well, the next week the retailer only orders five cases. Now the wholesaler is going to have way too much inventory which is tying up their cash flow and costing them money to store.
The wholesaler then doesn’t place an order at all with the distributor since they already have a ton of inventory. The next week the retailer comes in and orders sixty cases and the wholesaler doesn’t have enough.
As the wholesaler, you end up getting a chart that looks something like this showing how you performed.
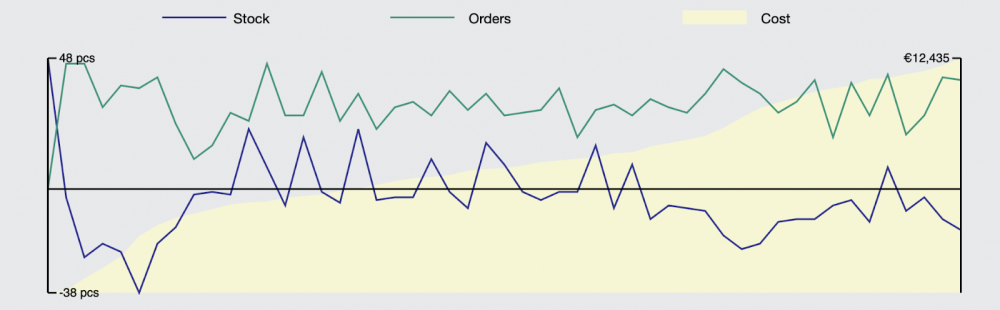
So there’s a bullwhip effect at each individual player’s level, but more perniciously, it whips up and down the chain.
The key learning from the beer game is that small changes in end demand can create huge imbalances as they move up and down the supply chain.
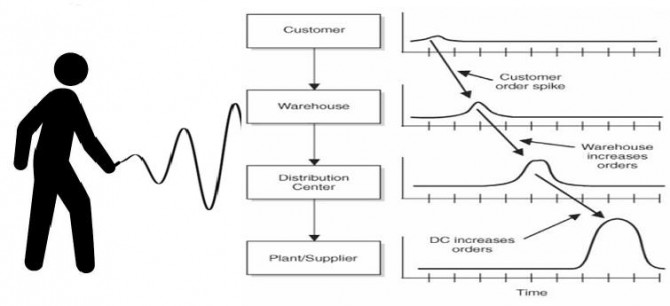
The game illustrates in a compelling way just how hard it is to run an efficient “just in time” supply chain, even for a relatively simple and idealized supply chain.
To manufacture an iPhone, Apple works with suppliers in 43 countries and six continents to make its products, and the supply chain gets even more complicated when you break it down into raw materials.
In all markets, suppliers, manufacturers, salespeople and customers often have an incomplete understanding of what the real demand of an order is.
Any “mistake” by one group can highly influence the entire supply chain by ordering too much or too little which can lead to a bullwhip effect: rotating between oversupply and undersupply.
To see a real-world example, look at the Lumber market from January of 2020 through July of 2021.
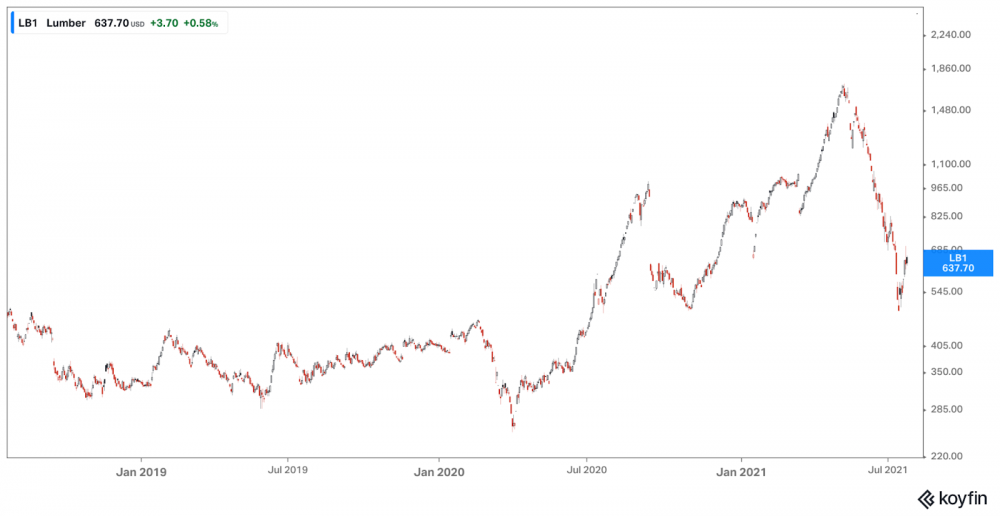
For a couple of years prior to 2020, the cost of lumber (as measured by the lumber futures contract) was pretty steadily in the $300-$450 range. As COVID came in and the world went into hibernation in the Spring of 2020, demand for lumber crashed and so the futures price came down below $300.
Suddenly demand for lumber for new housing skyrocketed and the price rose to over $1,000 in September of 2020. By October, it had dropped -50% to around $500. By May of 2021, it had climbed back up over 300% above $1,500 before falling to $500 again in July of 2021.
Looks like a Bullwhip doesn’t it?
It’s also important to understand that this real-world example is substantially more complex than the simplistic beer game. In the case of lumber, timber (the precursor to lumber) didn’t have a shortage and didn’t spike in price.
The bottleneck in the supply chain wasn’t growing trees, it was an intermediate step: sawmill capacity. Sawmills convert timber into usable lumber.
A temporary demand surge for new houses happened and sawmill capacity can’t expand overnight. It takes large capital investments and years to build a sawmill and so the price had to steadily rise to reflect the increased demand.
Deep supply shortages like growing more timber, building sawmills, or building new mines are far more complex than the beer game and take years rather than weeks to resolve.
The companies that work in those industries also aren’t likely to jump into solving them unless they have good reason to believe that the demand increase will last. If you build a new sawmill only to see demand return to historic levels when it’s completed then you just wasted a lot of money to build an empty sawmill.
Part of what COVID-19 did was it introduced a lot of volatility into both the demand and supply side of many goods and services. Demand for air travel in 2020 was as low as it has ever been and so airlines laid off many people and decommissioned planes. Demand came roaring back in 2021 and suddenly flights became more expensive and airlines got slammed.
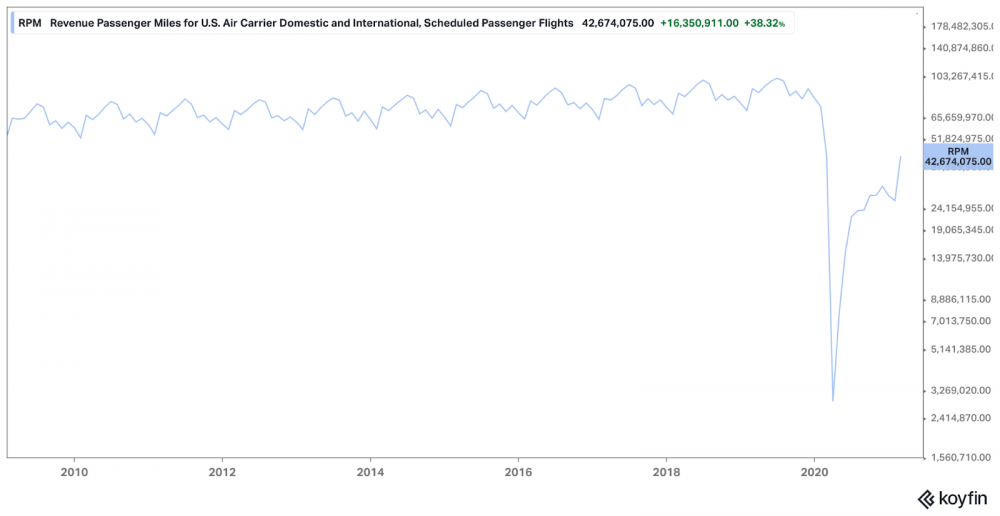
You can see the bullwhip effect pretty clearly in the data for Revenue Passenger Miles for U.S. Air Carriers – demand for the 8 years preceding 2020 was pretty steady with some typical season variation (historically, air travel in the U.S. tends to peak around July and bottom out in January).
This made it (relatively) easy to forecast so that airlines had the right equipment and personnel. That problem got a lot more difficult once that pattern broke.
Lumber and air travel are two specific examples, but the problem is much more general.
On a macro-level, one of the big shifts over the past few decades of globalization has been that supply chains got a lot longer, more complex and interconnected.
In one sense, this is a good thing: cheap transportation combined with large efficiencies of scale can make stuff cheaper. Instead of having lots of steel refineries all over the world, you have a few really big ones and, as long as trade flows freely, it makes steel cheaper (and subsequently everything that uses steel is cheaper).
In another sense, this is bad: if trade is disrupted or one major steel refinery shuts down due to, I dunno, say a global pandemic? Then that can reverberate across many different supply chains around the world.
It’s an example of the Robustness-Efficiency Trade-Off (RETO). Systems (systems used in the very general sense meaning it could be a project, company, country, society, etc.) must trade-off between being Robust and being Efficient.
Having a lot of smaller steel refineries is less efficient because you don’t get the same economies of scale that make costs lower, but it’s more robust in that any one refinery shutting down has less impact.
Having more steel refineries is more efficient because it makes costs lower when things are working well, but it’s also more fragile as any one refinery poses a greater “systemic risk.”
In Bullwhip Effect terms, that means that the world we live in today is a lot more efficient when things are “normal” but has much longer bullwhips with more potential imbalances when things get weird.
There seems to be some natural fluctuation between periods of increasing globalization (more efficiency, less robustness) and periods of increasing localization.
Global trade as a share of GDP rose throughout the 19th century and peaked in 1913. It declined with the First World War and didn’t reach its 1913 level again until 1979. We seem to be on (or heading towards) a similar down-trend with moves by the U.S. and other countries to bring more of their supply chains onshore (the leverage China had to hold back PPE shipments was a wake-up call).
On a more micro-level, the key lesson from the Bullwhip Effect is about the importance of better communication.
Individual Wal-Mart stores transmit point-of-sale data from the cash register back to corporate headquarters several times a day. This demand information is used to queue shipments from the Wal-Mart distribution center to the store and from the supplier to the Wal-Mart distribution center. By reducing the communication delay from weeks to minutes, Wal-Mart can get near-perfect visibility into customer demand and inventory movement throughout the supply chain.
Better information leads to better inventory positioning and lower costs throughout the supply chain.
For many businesses, the most important thing they can do is to push decision-making down the chain of command. Toyota’s Andon Cord was a rope that hung in Toyota factories. Nothing fancy, just rope like you’d use to tie down luggage to the roof of your car.
It was special in one way: when pulled, the rope would instantly stop all work on the Toyota assembly line.
If any human being in the manufacturing plant saw a problem with a car, they were required to pull the cord and stop the line.
Once all production was halted, a team leader would immediately go ask why the rope was pulled. Then, together, the leader and the team could work to solve the problem and restart production. Not only did they fix the problem, they figured out what was causing the problem so it didn’t happen again.
In Bullwhip Effect terms, they were able to catch the first “ripple” and solve it before it could whip down the line to cause larger problems. By pushing decision-making down the chain of command and improving communication, they reduced the bullwhip effect internally.
Last Updated on June 6, 2025 by Taylor Pearson